Design and Construction
By Jon Dunlap, M.SAME, Shawn Hanley, M.SAME, and Adrienne Wright, M.SAME
A pair of modular indoor firing ranges developed for two different federal agencies leveraged advancements in off-site construction and compartmentalized delivery to save time and funding despite logistics challenges, while also building flexibility that can meet future needs.
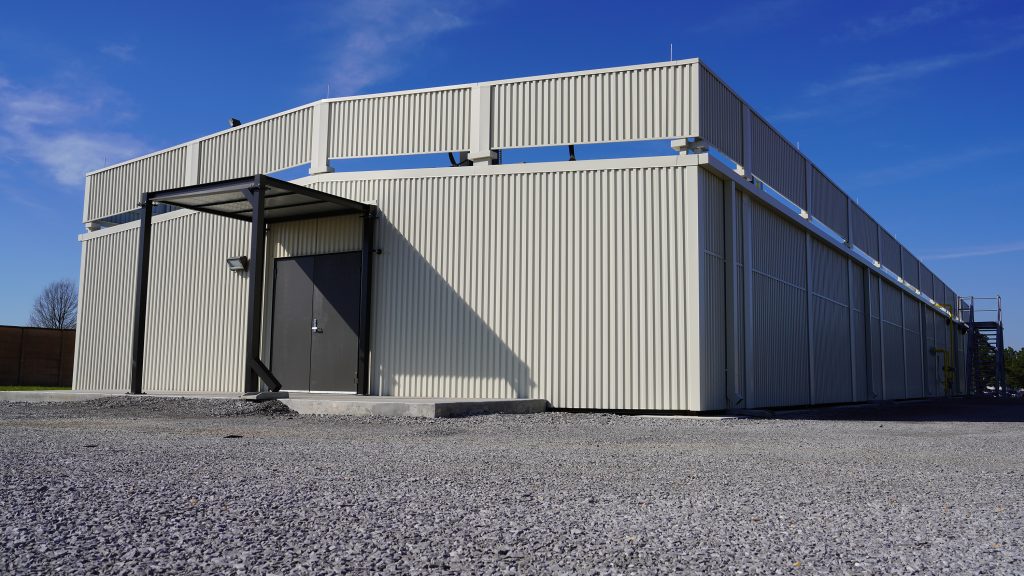
In early 2023, the U.S. Air Force unveiled a groundbreaking Modular Indoor Firing Range. This state-of-the-art facility, the first of its kind within Air Education & Training Command, sets new standards by meeting all requirements of associated Unified Facilities Criteria and serves as a blueprint for future firing ranges across the service.
With the design and construction of the Modular Indoor Firing Range (a collaboration between general contractor ESA South and modular firing range designer MILO LIVE), the Air Force will acquire comprehensive training opportunities that not only enhance convenience but also result in significant cost savings. By having the range now readily available at Columbus AFB, Miss., a key pilot training base, approximately $60,000 annually will be saved on commercial range fees and airmen will reclaim more than 500-hrs of drive time.
The modular indoor range, with its small footprint and innovative technical features, represents a significant advancement in military training infrastructure. The design process involved engineering, fabrication drawings, and calculations for the entire modular containerized firing range system, as well as coordinated delivery and setup logistics.
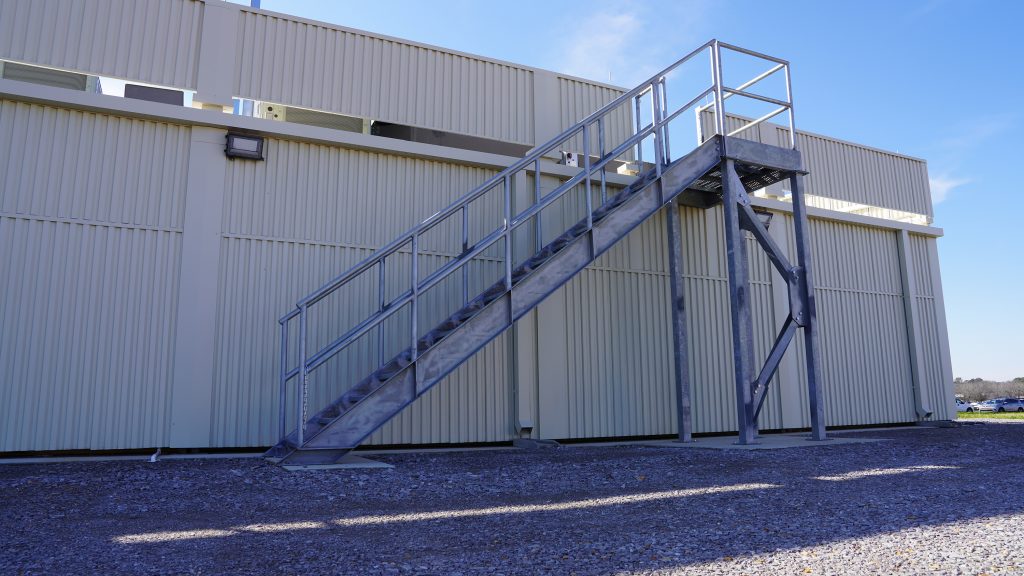
The project aimed to create a versatile and efficient training facility with various multi-user benefits, which are already being replicated at additional government locations.
Exacting Delivery
The fully operational seven-lane range was manufactured using relocatable modules, which ensured efficient production and assembly. The range has a wide-open design, bullet traps, a control room, seven extra-wide stalls, innovative shooting trays, acoustic materials, and unique target systems.
Executed under a contract initially awarded in July 2021, the structure was designed to be mobile and expandable in length, allowing for easy relocation and future expansion by adding additional modules. It features a roof-mounted HVAC system with stair access and perimeter edge fall protection.
In constructing the modular range, numerous complex components were required. Along with supplying all materials and labor, the project team needed to handle site demolition, preparation, grading, drainage, foundation and footings, and a retention pond. The scope of work also included connecting electrical utilities from a nearby transformer, connecting gas utilities from a nearby street access point, and extending the communications system from a central building on the base. Additionally, the team was responsible for landscaping the area, adding an access road, and expanding the paved parking lot.
The facility is made from 11 modules, which were built in Las Vegas. These modules needed to be delivered as oversized loads to the restricted-access military facility in northeastern Mississippi. The on-site team of 10 to 12 members spent around six months preparing the site before the 20-person installation crew arrived.
In order to carry out the delivery, coordination was needed with the base facility to shut down the main gate so that the modules could be trucked in through the exit gate. The entry gate was not wide enough for the oversized cargo. Timing was critical in order to remain mindful of the downtime imposed on the main gate as well as the overall production schedule.
Another significant challenge was ensuring that the site foundation met the specified tolerance for placing the modules. Each module sits on a concrete footing specifically designed and installed for the unit, and the components all needed to come together within a tolerance of a few millimeters.
Installation of the modules was completed in just 19 days without any major incidents. Given that, generally, when a project requires highly specialized items to be manufactured in different locations and brought together under a time-constrained schedule there is ample room for delivery to be disrupted, this was a win-win outcome.
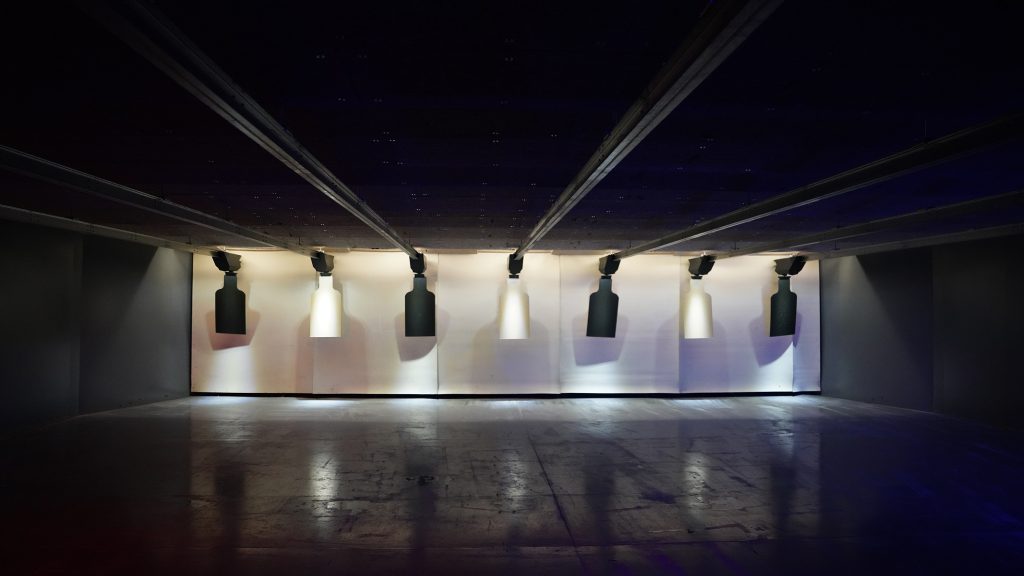
Building on Success
Looking ahead in 2024, ESA South and MILO Live are once again working to complete a modular shooting range. The client is the Immigration & Customs Enforcement Agency, under the Department of Homeland Security. The project has been awarded, designed, and is currently under construction.
This second modular shooting range facility is located on Crown Mountain, St. Thomas, in the U.S. Virgin Islands. Crown Mountain is a Four-Lane Ready Range “Tactical” Rifle-rated range with a 25-yd shooting distance. The facility consists of two bays, each equipped with two lanes, providing four lanes for versatile training. Designed for scalability, the range can be expanded in two-lane increments to accommodate future training needs. The range includes shooting stalls, target retrieval systems, bullet traps, programmable lighting, HVAC, and filtration systems. All materials were certified by an independent laboratory and designed to deliver value and long-term durability.
The delivery for the range included construction in Nevada and shipping to Crown Mountain for assembly following extensive site preparation. The design and construction teams addressed several challenges. To deliver them to the facility, the modules needed to be brought up the mountain, traversing a small, winding road. A great deal of coordination was needed to make certain the containers and trucks could successfully navigate this road.
Island weather often has created schedule delays due to frequent rain that would saturate the site and take additional time to drain and dry out. Additionally, the site contains many boulders that needed to be removed, and it also required leveling end to end.
The construction has required six crane lifts to place the modular pieces. Due to the length of the structures, a temporary road needed to be built to position the crane. The crane can be moved into multiple positions to reach the full length of the final placement. Once the lifts were completed, the road became a permanent addition to the project as requested by the owner.
For Mission Versatility
By leveraging the capabilities of off-site construction and modular delivery, these projects allowed two uniquely different government organizations to acquire modern training facilities at significant cost savings. Moreover, the range facilities are both flexible and scalable in design, which will be beneficial as the installations move forward with evolving responsibilities.
With these versatile training facilities in place, they will be ready to address future mission needs and ensure our federal agencies, and the people who work for them, remain always ready.
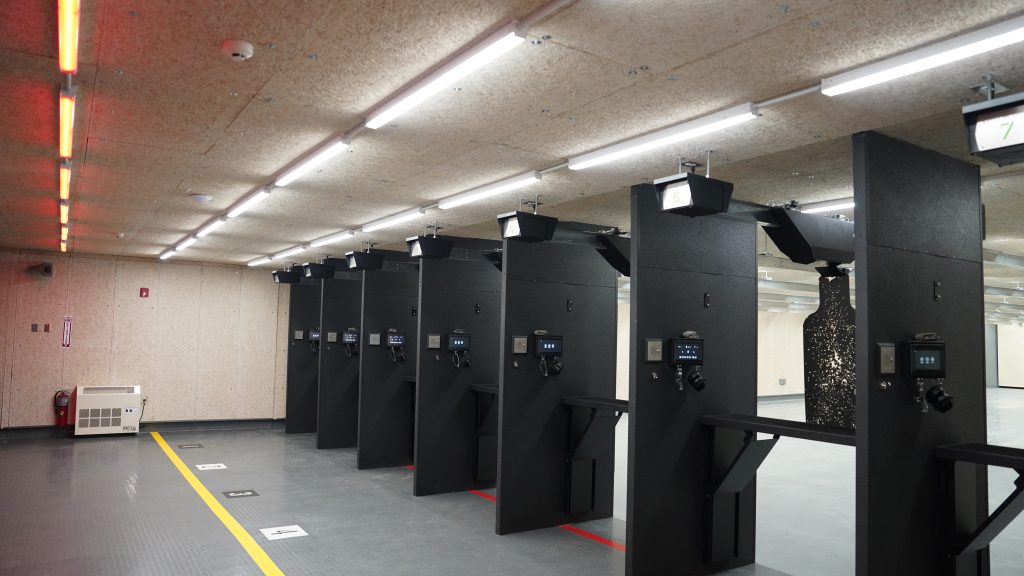
Jon Dunlap, M.SAME, is Director, Preconstruction and Estimating, Shawn Hanley, M.SAME, is Project Manager, and Adrienne Wright, M.SAME, is Marketing Director, ESA South. They can be reached at jdunlap@esasouth.com; shanley@esasouth.com; and awright@esasouth.com.
Article published in The Military Engineer, November-December 2024
More News from TME
-
Tracking Top A-E/Contracting Topics
A pair of recent reports detailing top-of-mind concerns for government contracting and architecture-engineering firms highlight areas of shared interest in the federal sector. -
Designing for the Unforeseeable
In the challenge of designing military buildings to resist progressive collapse, a revised technical approach offers a simplified way to arrive at a dependable estimate of material needed, potentially increasing cost controls on government projects. -
Revising the Arctic and Subarctic Design and Construction Guidelines
With a renewed focus on the Arctic and subarctic areas of the world due to evolving national security needs and changing environmental conditions, an effort to revise outdated construction and facility criteria for military infrastructure in these remote regions is well underway in preparation for future projects.